Overview
A major Illinois-based food processing plant processes hundreds of thousands of bushels of corn a day. Its safety and production functions have traditionally operated separately, leaving opportunities for improvement across its operational processes. SEAM Group – a global leader in reliability, safety, and maintenance – was chosen for this critical initiative because of its extensive experience integrating asset management efforts for major organizations.
Situation
SEAM Group was contacted to improve the company’s overall maintenance function. The engagement began with a robust advisory and strategy phase to identify critical gaps before morphing into the development of a multi-year maintenance process improvement plan.
The customer’s challenges included the following:
Preventive Maintenance – The customer’s preventive maintenance (PM) efforts were unorganized and largely manual. The CMMS was not properly utilized, resulting in inconsistencies in work plans and staff alignment.
Work Order Planning – Data was disparate, requiring time-consuming searches for key information that greatly reduced planner productivity. Information on a given critical machine could be found in a variety of places, including the company’s technical library, manuals, supervisor offices, or filing systems.
MRO Parts Management – The majority of equipment items did not have a valid Bill of Material in the CMMS. This led to usability issues with spare parts and non-preparedness when critical machinery went down
Solution
To tackle the aforementioned challenges, SEAM Group helped transform the company’s PM program, improved work order planning, scheduling, MRO parts management, and enhanced the utilization of its CMMS.
Here’s how:
Preventive Maintenance
SEAM Group utilized its preventive maintenance optimization application to create appropriate PM procedures and intervals for standard industrial machinery. This greatly facilitated the completion of tasks and processes. SEAM Group also improved the flow of all PM procedures for client reliability engineers before being reviewed by planners and technicians.
Results:
- Enhanced the utilization of the CMMS to schedule PM activities
- Dramatically reduced the company’s asset downtime
- Better leveraged PM work order history and technician feedback
Work Order Planning
A planner can now leverage the equipment BOM to check the status of parts needed for an equipment repair quickly, allowing the planner to orchestrate more work orders. By knowing the parts needed and their status, the planner can better determine scheduling readiness.
Results:
- Improved work order planning and scheduling
- Boosted maintenance technician efficiencies
- Better utilized scheduled downtime
MRO Parts Management
SEAM Group ensured a more comprehensive approach, combining the Bills of Materials in CMMS with the storeroom MRO inventory and plant equipment. The integration allows the CMMS to analyze the number of parts required to support operations.
Results:
- Better data accessibility to enable more efficient PM activities
- Allowed deletion of duplicate or non-essential parts
- Drove immediate cost savings due to improved business efficiencies
A Proven, Reliable Framework
SEAM Group followed a reliability program implementation methodology to improve maintenance strategies and asset performance outlined below:
- Developed PMs and job plans for maintainable equipment based on the asset criticality
- Reviewed with client and finalized maintenance plans
- Prepared approved PMs and job plan in a CMMS load-ready format
Provided MRO (Maintenance, Repair, & Operations) subject mater expert (SME) resources to lead and assist client personnel in improvement activities focused primarily within the inventory management EAM elements outlined below:
- MRO Bill of Materials / Critical spares Identification
- MRO inventory management stocking strategies
Share
Preventative Maintenance Results
- Enhanced the utilization of the CMMS to schedule PM activities
- Dramatically reduced the company’s asset downtime
- Better leveraged PM work order history and technician feedback
Work Order Planning Results:
- Improved work order planning and scheduling
- Boosted maintenance technician efficiencies
- Better utilized scheduled downtime
MRO Parts Management Results:
- Better data accessibility to enable more efficient PM activities
- Allowed deletion of duplicate or non-essential parts
- Drove immediate cost savings due to improved business efficiencies
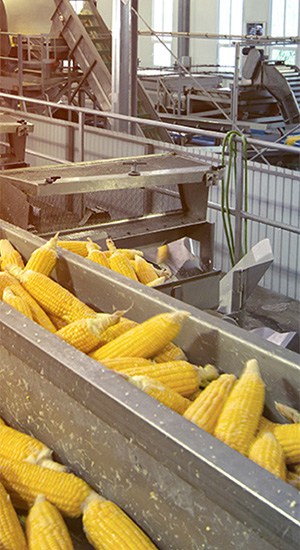