If you are in an asset-intensive business, you know the importance of having a comprehensive approach to asset reliability, safety, and maintenance. Gaps in asset management and optimization can lead to unplanned downtime for reactive maintenance, missed commitments, lower profit margins, and a negative impact on your asset’s life and performance.
Read on to learn how asset reliability consultants can provide tremendous value to your business.
What is asset maintenance reliability?
You rely on your assets to meet your production goals, so maximizing asset availability directly connects with revenue generation and profitability. Asset Reliability focuses on optimizing the design, operation, maintenance, and sustainability of an asset to ensure that it performs to expected levels throughout its useful life with minimal downtime at the lowest financial and environmental costs. Properly defined asset reliability covers the entire lifecycle, from delivery to decommissioning or cradle to grave.
How do you determine the reliability of an asset?
Some KPIs and factors contribute to evaluating asset reliability. There are standard analytics that give you insights, as well as unique attributes depending on the asset classification to determine reliability. Many of today’s software tools support measuring technical indicators for asset reliability from performance data such as downtime, mean time to repair, and mean time to failure.
The Goals and Benefits of Asset Management Consultancy
Reliability consultants take several factors into account when creating a maintenance strategy. They seek to protect the facility’s asset investment, encourage consistent performance, and minimize asset downtime.
- Improving Asset Reliability
Every asset has a limited usable life. Some machines will operate for years without incident, and others seem to break down every week. A reliability consultant develops a maintenance plan where individual assets receive the care they need to avoid disrupting production. They will also examine operational factors where changes might increase reliability. For example, slowing the rate of an engine may prevent periodic overheating.
- Risk Assessment
Part of the job of the reliability consultancy team is minimizing the risk of losing a critical asset. Understanding the risk is more than just knowing the asset’s reliability. It also involves understanding the entire asset ecosystem. The consultant will look at the inventory of spare parts as well as supply chain issues like the health of third-party suppliers.
- Optimal Asset Performance
Equipment failure often comes from running a machine outside its ideal operating parameters. The consultant will determine the conditions that lead to consistent, optimal performance.
- Increased Asset Longevity
Businesses have a better ROI when equipment lasts longer than expected. In most cases, an ideal maintenance strategy will increase asset longevity. Equipment that receives optimal care will run longer without significant performance issues.
- Maintenance Strategy Development
The primary goal of asset management consultancy is a workable maintenance plan that enhances asset performance and reliability. This plan will include an optimized list of maintenance tasks, a suggested spare part inventory, and a list of ideal operating parameters for each asset. It will also list out the criticality of each asset, helping the facility determine priorities when there are limited resources.
Determining Asset Reliability
Improving the consistent performance of an asset is an essential part of a reliability consultant’s task. A successful plan requires an understanding of general asset reliability.
Mean Time to Repair
The Mean Time to Repair (MTTR) is a metric used when looking at the ability of a maintenance team to address breakdowns. Consultants calculate this measurement by dividing the total offline repair time by the number of repairs in a given period.
For example, a couple of common reliability metrics are:
Mean time to repair, or MTTR, measures a department’s ability to respond to a downed asset and restore it to optimal working conditions. This simple metric is a strong indicator of an organization’s overall reliability program and maintenance preparedness as it is impacted by several key aspects such as:
- Having the correct parts when a failure occurs
- Having the proper tools for maintenance activities
- Having available resources and personnel to respond quickly to asset failures
Mean Time Between Failures
The Mean Time Between Failures (MTBF) is another measurement used in determining reliability. To calculate this number, the consultant divides the total operating time by the number of failures.
Another necessary measurement that asset reliability consultants consider is the mean time between failures, MTBF. This calculation divides the equipment’s operating time by the total number of failures experienced over the same period. MTBF is used quite frequently in asset maintenance and reliability work. This metric provides insight into the asset reliability and maintenance plan the asset.
Areas that impact MTFB:
- Design elements that contribute to premature failures
- The effectiveness of the preventive maintenance plan and schedule for the asset
- The quality of the parts utilized to maintain the asset
- The experience and knowledge of the personnel working on the asset to correctly perform maintenance
Asset Availability
Dividing the MTBF by the sum of the MTBF and the MTTR results in a measurement of availability. Most facilities want their assets available at least 95 percent of the time. Critical assets need an even higher percentage of availability.
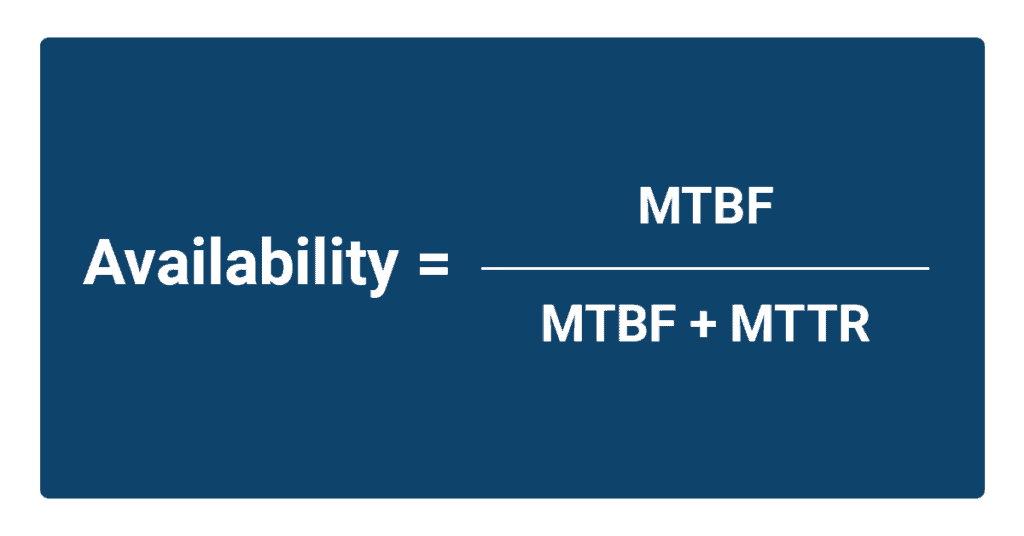
Areas that impact Availability:
- Design elements that contribute to premature failures
- The effectiveness of the preventive maintenance plan and schedule for the asset
- The quality of the parts utilized to maintain the asset
- The experience and knowledge of the personnel working on the asset to correctly perform maintenance
How do you measure asset reliability?
Once you have the MTTR and MTBF of any equipment, you can determine its availability, also known as the amount of uptime or running time. You’ll get availability by dividing the MTBF by its MTBF plus MTTR. Most business assets need to have an availability of at least 95 percent. Mission-critical assets typically demand a higher availability percentage. Economic indicators also provide insight into the asset cost and performance at its current stage in its lifecycle. All these factors can be combined into overall asset health, empowering decisions surrounding the assets’ reliability and overall lifecycle optimization.
How can you improve asset integrity?
Enhancing the reliability of your business assets is dependent on your asset strategies and maintenance programs. Optimized maintenance activities and utilization of available technology can keep equipment availability high to meet your production needs while managing costs.
Working with an asset integrity management specialist, you can quickly determine your current state, identify key opportunities, and optimize maintenance activities while planning for asset replacement needs relying on key metrics like asset availability. You can eliminate the guesswork in asset management when you partner with an experienced subject matter expert to develop and implement a strategic maintenance approach.
Common Asset Performance Strategies
Consultants may recommend several strategies for improving asset reliability. The type of required care will depend on the criticality and complexity of the asset.
- Run to Failure: This reactive strategy is appropriate for low-priority assets or those designed for replacement. The maintenance team waits until the equipment fails and then repairs or replaces it.
- Preventive Maintenance: Machines with moving parts often require scheduled maintenance tasks like lubrication. Frequently, manufacturers provide a recommended schedule for technicians.
- Predictive Maintenance: A predictive approach employs sensors to gather data about asset operational performance. This real-time information lets maintenance staff observe changes in efficiency and productivity. They can address the situation when the performance veers too far outside the norm.
- Prescriptive Maintenance: A prescriptive asset maintenance and reliability strategy may be the right approach for complex, mission-critical equipment. It seeks to determine ideal operational parameters as well as regular maintenance tasks. Consultants will assess this plan using resources such as manufacturer recommendations and operational data.
How can asset reliability consultants help?
Asset reliability consultants determine a particular asset’s criticality and reliability and optimize maintenance activities to allow you to better utilize resources when bandwidth is an issue. They have the knowledge and experience to evaluate your assets and develop a reliability and maintenance program tailored to your goals and KPIs.
The main goal of hiring an asset reliability consultant is to optimize the entire lifecycle of your critical assets. Partner with our expert consulting team to access our decades of experience across industries.
SEAM Group is a global asset operation management company that offers asset safety, reliability, and maintenance for businesses worldwide.
Call us at 866.772.6770 to discover how we can assist you with asset reliability to deliver mission-critical outcomes for your people and shareholders.