Safety Consulting
A partner for your asset optimization journey
Unlike traditional consultants, we help you lead field implementation with a tailored road map and disciplined execution while connecting safety, maintenance, and reliability to deliver mission-critical outcomes.
Industry leaders found four main challenges in the asset optimization journey, including:
- Implement a Risk-Based Reliability & Safety Strategy
- Align & Optimize
- Deliver Consistency Across Locations
- Accelerate Outcomes
- Life Cycle Asset Management (LCAM)
- Asset Performance Optimization
- Reliability Program Implementation
- Safety and Maintenance Compliance
Book Your Consultation Today!
Case Study: Global Food Processor Company
Customer Goals:
- Gain end-to-end visibility of CAPEX and OPEX costs.
- Fully understand OPEX costs which account for 80-90% of asset lifecycle costs.
- Rely on a tool to guide TCO decision-making and overall cost reduction.
Solution:
- SEAM Group developed a TCO tool allowing the customer to run through various ‘what if’ investment scenarios.
- “Hidden” OPEX costs were evaluated, including suppliers and supply chain impacts on margin.
- Stage gate and governance were established in conjunction with the company’s One Engineering operating model.
- Pilot training program to establish roles, responsibilities, and decision-making criteria.
- Training was rolled out to an extended core team, including engineering and S&F.
Winning Results:
Delivered $74M of cost avoidance savings on a $1.2B annual spend
Identified an additional $50M in cost avoidance savings for existing assets.
Case Study:
Global Life Science Company
Customer Goals:
Develop a streamlined and efficient approach to capitalize on the company’s resources.
The intricacies of executing a CAPEX project with multiple stakeholders and a complex process flow inadvertently hindered the utilization of valuable expertise and experience that could enhance the reliability, availability, safety, and maintainability of equipment.
Solution:
Implementing a standardized Design for Reliability (DfR) process, SEAM Group meticulously crafted checklists tailored to more than 50 equipment classes. Our primary emphasis was on bolstering “shop floor” efficiency and overall reliability.
SEAM Group formulated operational readiness checklists for every equipment class, ensuring a comprehensive approach to optimizing performance and operational readiness.
Winning Results:
Our experts eliminated the risk of multiple failures, quality discrepancies, and challenges related to reliability. The approach also extends to future CAPEX projects, where a standardized process is utilized and augmented by the active engagement of both operations and maintenance at specific project checkpoints.
This strategy mitigates pitfalls and establishes a robust framework for long-term success.
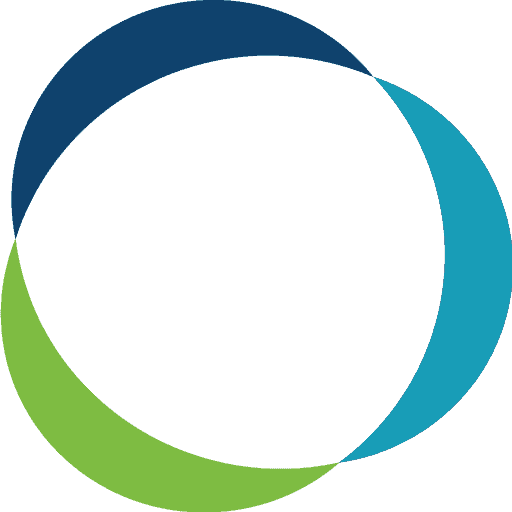
The SEAM Group Difference
Collaboration and Partnership Defined
More than a vendor, SEAM Group functions as a strategic advisor to meet you where you are and take you where you need to be. We uncover quick wins, while also developing and managing long-term programs to help you exceed ongoing safety, reliability, and maintenance goals.