Arek Burnos, Managing Director of EMEA, shares answers to frequently asked questions regarding maintenance costs and the benefits of optimization.
Is maintenance often perceived as a cost in your organization?
Many companies perceive maintenance as a cost that needs to be reduced as much as possible. Still, we believe that maintenance spending can deliver improved financial, reliability, and safety outcomes if managed correctly.
- Reliability as a metric is the result of a system’s design, construction, and how it is maintained and operated.
- Reliability as a process focuses on making economic and safety-driven decisions to improve resource allocation for equipment and facilities.
When you operate facilities and equipment, optimized maintenance is necessary to achieve reliability which is key to your operational goals.
When you think of reliability as a process focused on economic and safety outcomes, then the way you spend money on equipment and facilities will be viewed as an investment, not a cost. An effective reliability loop ensures you have a maintenance optimization strategy and well-defined KPIs for each one of your assets, which in turn leads to reduced waste, increased uptime, and better safety outcomes.
What is the financial impact of an incomplete or broken reliability loop?
A missing or incomplete reliability loop process inevitably leads to extensive equipment downtime, safety accidents, slow processes, and quality misses. Operational failures can lead to long-term shutdowns, asset decommissioning, compliance costs, and lost customers in the most severe instances.
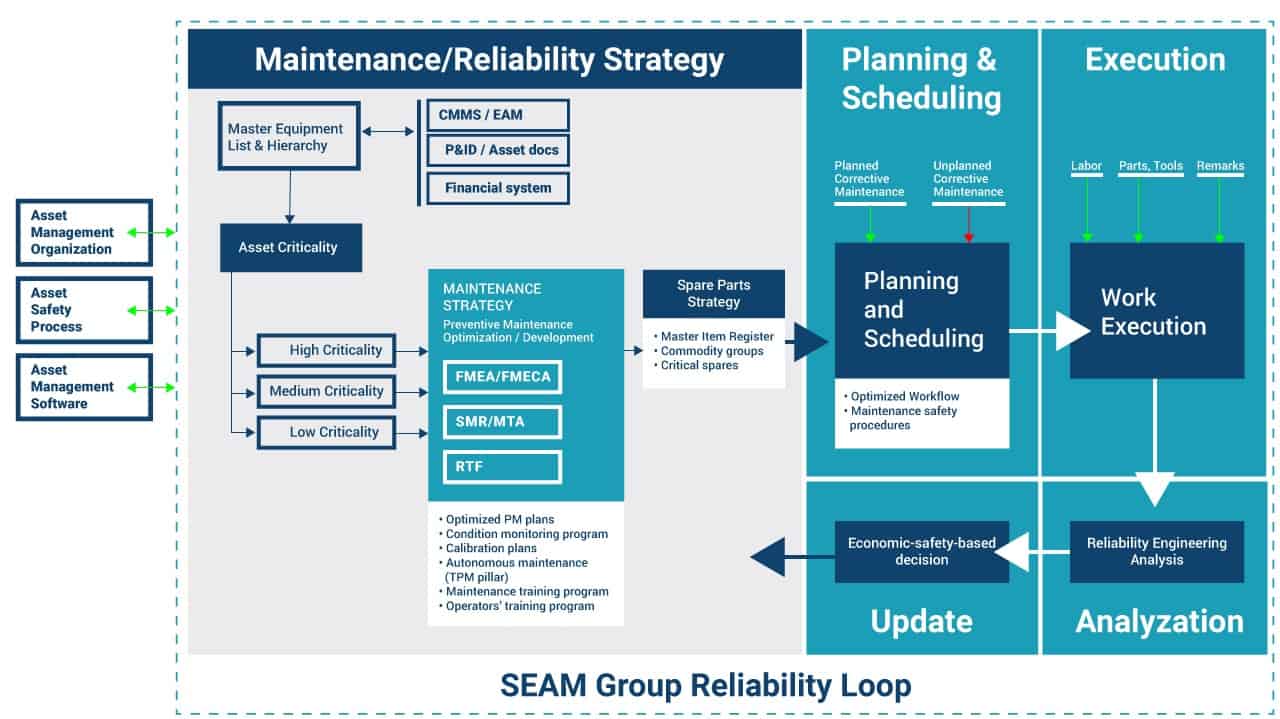
Is there any way to counteract the increased cost of maintenance driven by inflation?
The short answer is yes! We have identified more than 20 short and long-term direct cost optimization categories in maintenance and reliability areas. We find many of our clients can control costs by focusing on maintenance productivity, avoidance of failures caused by raw materials, and better control of spare parts. Other organizations have significant potential in reviewing contracts and consolidating contractors. Customers with high failure rates need to focus on reliability basics driven by criticality risk assessment to optimize preventive maintenance.
Are there quick wins SEAM Group can recommend?
At SEAM Group, we make things systemic and easy for our clients. When looking at quick wins, many of our clients will start maintenance optimization for a specific line or department. This controlled exercise proves maintenance optimization’s benefits in less than a quarter.
Why is an asset management system needed?
Your managers should be able to ask data-based questions to identify asset class and maintenance process gaps. The example we like to use in our maintenance management courses is the following: If you have one car, it’s easy to keep track of its components, maintenance, age, location, use stats, upgrades, driver profile, etc. Now, imagine doing the same thing for 1,000 cars! You will need a system, an asset management system with proper controls.
Why use a CMMS/EAM system instead of Excel to manage so much data?
Many companies still use Excel sheets as their maintenance and reliability IT systems in the absence of proper CMMS/EAM software. A CMMS/EAM system with the right integrations, trained users, reliable master data, and reporting/business intelligence capabilities enables companies to utilize the data from their assets. CMMS/EAM systems can also be used with other systems supporting early asset life cycle stages like CAPEX planning, risk assessment, construction, and commissioning.
Where to start?
Get your maintenance stakeholders together and develop a short and long-term plan at the site, regional and global levels. Make it simple and practical. This process will result in a portfolio of actions and projects you can execute.
We see teams around the globe taking intensive cost-cutting actions due to current market conditions. However, it would be best to consider the associated risks and long-term impact these cuts have on asset life. The companies that made investments and maintenance overhauls during a market slowdown immediately saw benefits from their investment.
Key points we encourage you to think about:
- What savings can you realize through pure waste elimination?
- What must not be cut because of the associated risks?
- Areas where it is time to invest with upgrades, renovations, and replacements
SEAM Group can support all organizations looking to optimize their maintenance activities, reduce operating costs and ultimately improve reliability across their assets.
Why SEAM Group?
Great question! With so many consultants in the market, what sets us apart is our integrated approach that includes program development, engineering implementation, and field deployment. We know how to get effective results, not just create plans. We build on this by using a cooperative model in which we lead the completion of deliverables by working with your team to leverage their insights and knowledge. We don’t view ourselves as temporary players and continuously strive to add value to performance and process results.
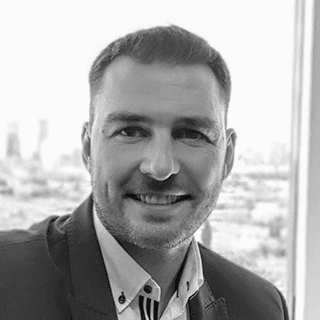
Arkadiusz (Arek) Burnos is the Managing Director for Europe, the Middle East, and Africa at SEAM Group. He drives the growth and business operations spanning asset management, condition monitoring, and safety services.
Arek has more than a decade of experience managing complex asset management and industrial maintenance projects for companies across multiple industries.
Let’s talk!
Arek Burnos
[email protected]
T: +48 22 20 35 440 | M: +48.505.173.493