Lock Out Tag Out Procedures
SEAM Group ensures your LOTO procedures comply with OSHA 1910.147. Our experts assess, report, and provide actionable insights for a safer workplace.
Enlist our support to build or enhance your Lockout Tagout (LOTO) program, including digital lockout/tagout. Properly documented and implemented lockout tagout procedures can help prevent unexpected energization or release of hazardous energy during maintenance activities.
Lock Out Tag Out Procedure Development
- Acquire and review your asset list
- Field verification of assets and identification of energy isolation points (EIP) for each asset
- Apply labels with unique QR codes to each energy isolation point to provide access to relevant procedures at the point of work and prevent errors during servicing and maintenance
- Quality check by a senior safety expert to ensure information and procedures match field verification and QR codes work correctly
You’ll notice immediate, high-impact benefits, including:
- Enhanced critical procedures to prevent near misses and recordables
- Avoid regulatory and compliance-related citations
- A structured LOTO strategy across your organization
- Better education for employees on LOTO hazards
- Proper energy isolation of equipment
- Safer equipment servicing and maintenance
Improve the safety and compliance of your lock out tag out procedures
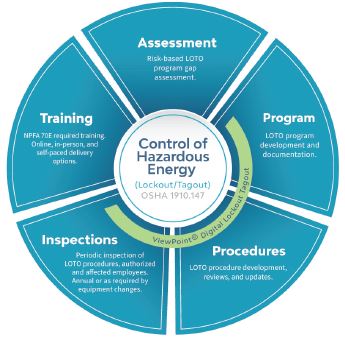
OSHA Violation Costs
The cost and effects of a workplace injury go beyond claims and fines. A serious OSHA violation penalty can be up to $15,625.
The penalty for a willful or repeated violation can be up to 10x higher! $156,259.
Average Claim Cost
The average cost of a workplace injury claim is $41,353. It is conservatively estimated that for every dollar spent on workers' compensation, you can spend $2.12 on indirect costs.
Actual Cost
$41,353 + ($41,353 x $2.12) = $129.021 (Actual cost)
If your company operates at a 10% profit margin, you will need an additional $1,290,000 in revenue to pay for the injury.
The Components of a Successful Lockout Tagout Program
The first step in the development of a successful Lockout Tagout program is documenting the LOTO energy control process within your facility. Each program must be customized for compliance with the applicable OSHA regulations and standards, as well as your company’s specific requirements and policies.
The documentation needs to include clear energy control procedures (ECP) for affixing appropriate lockout and/or tagout devices to energy isolation devices:
- Process review and data collection
- Energy control procedure (ECP) development
- Final review and delivery
If you already have a LOTO program in place, our team can perform a LOTO Compliance Gap Assessment to identify improvement opportunities and make recommendations.
Of course, the power of your Lockout Tagout program investment is unlocked when your people are properly trained, and empowered with the skills to do their job safely. You can rely on our safety training expertise to meet compliance requirements, and to advance the capabilities of your team with lockout tagout training.
Working with us also means you’ll enjoy the wide-ranging benefits of ViewPoint – our simple, scalable technology solution that provides rich data insights into asset performance and health. So, whether you are looking to build, assess, or digitize your Lockout/Tagout and critical procedures program, our goal is to help you build a safer, more reliable work environment.
A scalable solution for any industry
No matter your industry, SEAM Group can enhance your safety, reliability, and maintenance capabilities.
Uptime, safety and productivity issues can have negative effects on your overall operations, team performance, and reputation in the marketplace.
Companies in this industry have been hit hard by the pandemic and require robust safety, reliability, and maintenance plans to ensure uptime of facilities in order to meet increasing customer demands.
As the world turns digital-first, maintaining the safety and reliability of key equipment and data centers is the key to meeting customer uptime and SLA requirements.
Compliance, reliability, safety, and speed to market are key components for success in the Life Sciences space. Through our unique mix of services and solutions, SEAM Group has you covered.
The property management sector requires comprehensive inspection and maintenance services to deliver key outcomes such as compliance, reduced risk of fire or electrical outage, and enhanced customer experience to drive occupancy rates.
A reliable, safe and risk reduced operations is the key to running a successful oil and gas business. Let SEAM Group solutions drive you to these outcomes.
Your employees and guests deserve confidence in the safety, reliability, and maintenance of your facilities. Give it to them with our expertise.
Insurance companies should be focused on reducing their overall risk exposure to ensure customer satisfaction and team effectiveness.
With hundreds and sometimes millions of people depending on clean water and well-functioning power, the overall quality is key.
From charging station reliability to pre-build site plan assessments, we are experts in ensuring the optimal utilization of your equipment.
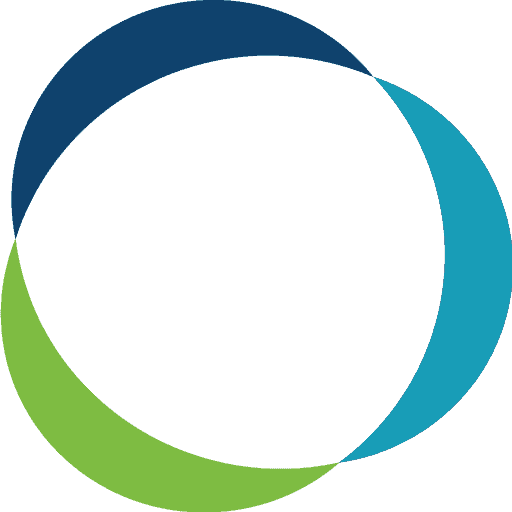
The SEAM Group Difference
Collaboration and Partnership Defined
More than a vendor, SEAM Group functions as a strategic advisor to meet you where you are and take you where you need to be. We uncover quick wins, while also developing and managing long-term programs to help you exceed ongoing safety, reliability, and maintenance goals.
Related Content
Taking a Deep Dive into the World of LOTO
Article Originally Featured in Occupational Health & Safety (OH&S) Author: Bret Bevis, SEAM Group Program Manager – Infrared & ViewPoint Procedures must keep pace with
NFPA 70E® Training Considerations to Move Electrical Workplace Safety Forward
To protect employees from electrical-related injuries, the National Fire Protection Association (NFPA) has developed the Standard for Electrical Safety in the Workplace® known as NFPA
Developing a Safer, More Effective Lockout/Tagout Program
Energy sources such as electricity, chemical, pneumatic, hydraulic, mechanical and many others can be hazardous to workers. During the servicing and maintenance of machines and